Coil Transfer Trolley: Extreme Temperature Battery Life Guarantee
Battery Life Guarantee
At low temperatures, the viscosity of the electrolyte in lithium batteries increases and the migration rate of lithium ions decreases, resulting in a loss of battery capacity and a reduction in charging and discharging efficiency.
In order to cope with this problem, coil transfer trolley is usually equipped with an intelligent heating system. The system preheats the battery pack through a built-in heating film or wire to maintain the battery temperature in the appropriate operating range, generally 5℃ – 35℃. At the same time, the use of electrolyte and electrode materials with excellent low-temperature performance, such as adding special low-temperature additives to the electrolyte to improve the conductivity of lithium ions.
The use of anode materials with high lithium embedded capacity and good low-temperature cycling stability, such as carbon nanotubes composite anode, to effectively enhance the battery’s charging and discharging performance at low temperatures.
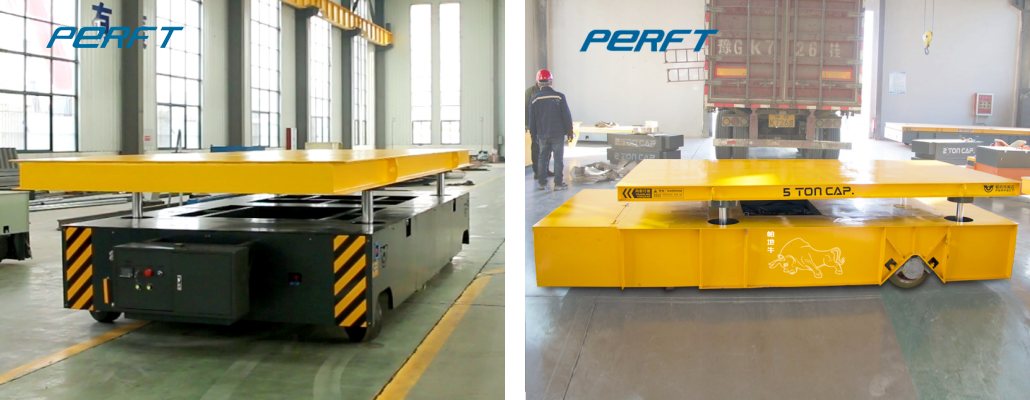
In a high-temperature environment, batteries are prone to overheating, which accelerates battery aging and even leads to potential safety hazards.
For this reason, most coil transfer trolley adopts liquid cooling or air cooling system. Liquid cooling system takes away heat by circulating coolant in the battery pack, which has high cooling efficiency and uniform temperature control.
Air cooling system utilizes fan-forced convection to accelerate air flow and take away heat. In addition, the advanced battery management system (BMS) monitors the temperature, voltage, current and other parameters of the battery in real time, and automatically adjusts the charging current and discharging power when the temperature is too high, avoiding the battery from being in a high-temperature and high-load state for a long period of time, prolonging the battery’s service life, and guaranteeing the range.
Self Propelled Transport 20 Ton Video
Vehicle Structure Protection
Low temperature makes metal materials brittle and reduces the toughness and strength of the body structure. In order to ensure safety, coil transfer trolley uses low-temperature-resistant alloy steel or aluminum alloy materials at the design stage, which can still maintain good mechanical properties at low temperatures.
At the same time, we optimize the structural design of transfer trolley body by adopting a more reasonable stress distribution structure, increasing the reinforcement and support structure in key areas to disperse and cushion the external impact force, and reducing the risk of structural damage due to brittle materials.
The challenge of high-temperature environments for transfer trolley body structures lies mainly in the thermal expansion of materials and the deformation of components. In this regard, during the manufacturing process, a reasonable thermal expansion gap is reserved to prevent parts from being damaged due to thermal expansion and contraction by squeezing each other.
For materials that are susceptible to high temperatures, such as rubber seals and plastic parts, special materials that are resistant to high temperatures and aging are used to ensure the sealing of the body of electric transfer trolley and the integrity of the components. In addition, special coatings are applied to the surface of the body, such as spraying high-temperature-resistant anticorrosive coatings, which can effectively reflect heat and reduce the surface temperature of electric transfer trolley, as well as prevent corrosion under high-temperature and high-humidity environments, thus guaranteeing the long-term stability of the body structure.
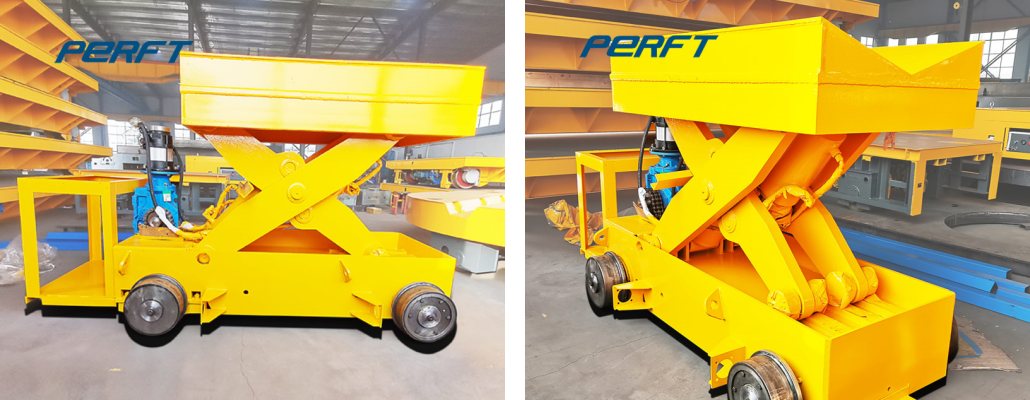
Through targeted technical improvements and optimization of the battery system and vehicle structure, coil transfer trolley is able to achieve double protection of battery life and vehicle structure in extreme high and low temperature environments, providing reliable support for the continuity and stability of industrial production.
Back to List